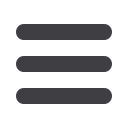
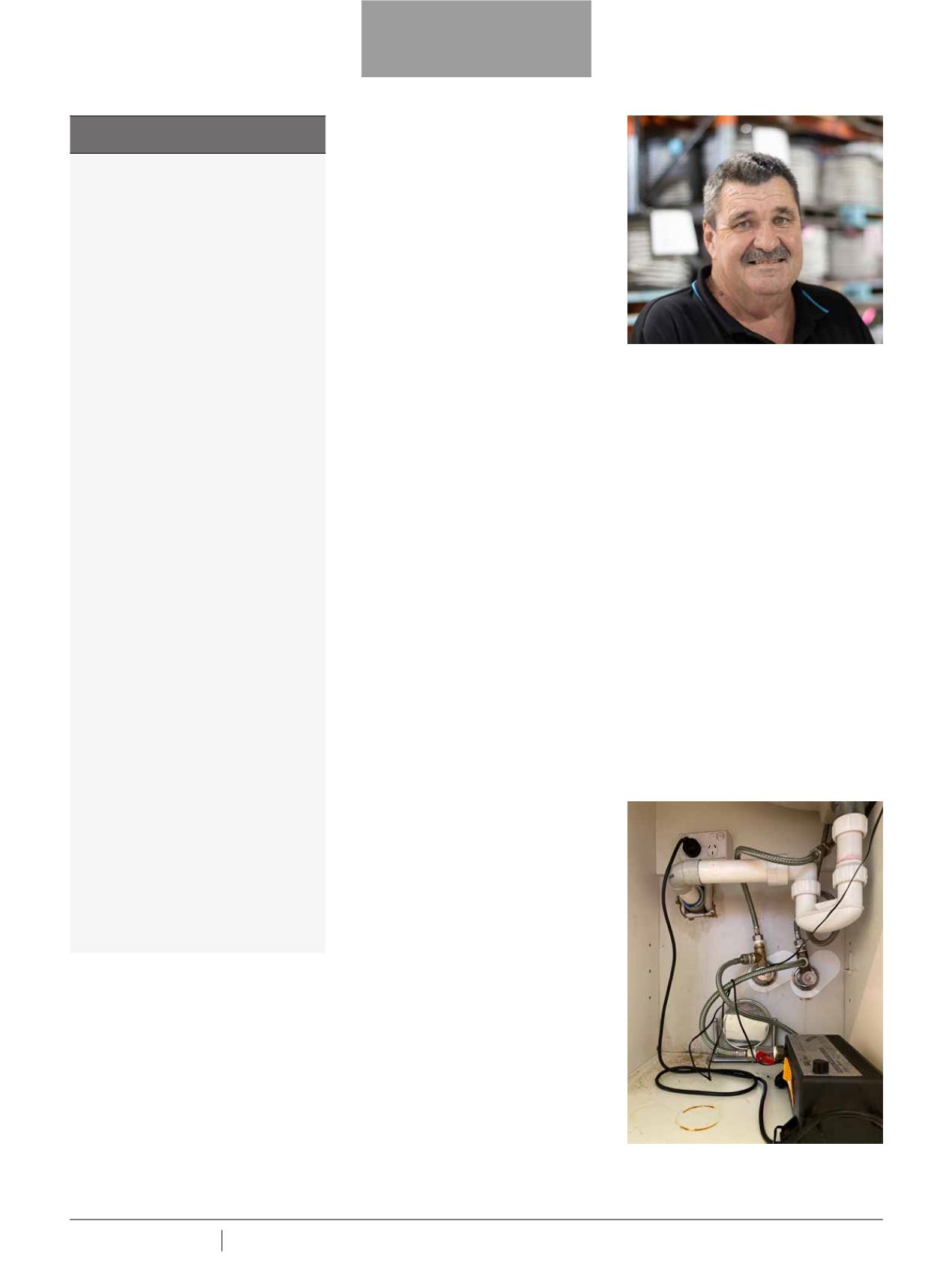
1 6
PLUMBING CONNECTION Winter 2022
“There are inferior products that
continue to enter the country,” Michael
laments. “Overseas manufacturers
secure distribution down here through
a distributor, and what happens is they
start making the product cheaper –
they start taking the brass out of nuts,
making them lighter, or using a lesser-
diameter stainless braid. When you look
at some of these items, the actual nuts
only engage by two-to-three threads:
what they’re doing is removing some of
the key costs from the manufactured
product.”
WIDESPREAD DEFICIENCIES
Let’s look in turn at various product
deficiencies affecting the three main
hose elements: sleeves, tubes, and
connectors.
The braided sleeve is what holds
the inner tube together and prevents
it from bursting or herniating under
pressure. Braid designs are uniform,
through the wire gauge, its quality, and
the consistency and angles of the weave
can vary tremendously.
As an example of manufacturing
tolerances of high-quality fittings,
Michael notes his own company’s
insistence on the use of 0.23mm
stainless steel wire for making the
braided sleeve for a typical hose, on the
basis that a greater thickness covers
more surface area.
“By contrast, the smallest of our
competitors’ products, we’ve found,
is 0.13mm,” he says, explaining that
Aquaknect routinely tests rival products
for compliance.
There is a critical issue with the
braid, he adds. The braid angle must
be exact because the inner tube, while
being able to move under different
pressures, should not cause the
surrounding sleeve to elongate and
expose a weak spot. An ideal weave
angle of 60 degrees is considered
necessary for long-term, reliable
performance. “But I’ve seen braids on
product that is available in Australia
that are flat, i.e. sitting at 80-90
degrees, so as soon as that hose starts
to build up pressure, the braid doesn’t
move. The inner tube will then find a
weak spot within the braid and herniate
out and blow.”
The integrity of the inner tube is
equally important to overall product
performance. There are two main
material options – EPDM rubber or PEX
– used for manufacturing Flexi Hoses.
Michael says Aquaknect uses only
Australian-made EPDM rubber, which
he says is superior to PEX for both hot
and cold water applications (up to 180
degrees Celsius.) “Some of the PEX
hoses don’t handle hot water very well,”
he notes. “When PEX first came out
there was PEX A, which was very rigid:
if you took it above 90 degrees it would
kink and form an extreme weak spot.
Then PEX B came out, which is more
flexible but nowhere near as flexible as
EPDM rubber.” PEX hose has another
problem, he says, which is a ‘memory’,
COVER STORY
FLEXI HOSES
Michael Glover from Aquaknect Flexibles.
COMMUNITY ATTITUDES TOWARDS POOR-
QUALITY FLEXI HOSES
Public attitudes towards poor-quality Flexi
Hoses are extreme and varied, highlighting
the complexity of reforming the category.
The insurance industry, for instance,
currently takes a lenient approach towards
poor-quality product: “Generally, we would not
decline a claim if it was non-compliant with
WaterMark standards,” a spokesperson from
IAG Insurance told
Plumbing Connection.
This
kind of acceptance, no doubt based on
customers’ convenience and unquestioning
capacity to pay higher premiums, could
change at any moment, as we have seen
already with certain building products such
as façade cladding: some insurers no longer
honour claims involving damage arising
from non-compliant, flammable materials.
Also, there is nothing stopping insurers from
offering cheaper premiums to owners of
properties with demonstrably superior fittings,
perhaps underpinned by a more sophisticated
and detailed construction sign-off than
existing ‘compulsory’ regulations deliver! Food
for thought if you are an insurer!
Other agencies are less forgiving. For
instance, at the time of writing, South
Australia’s Department of Infrastructure
and Transport is refining a draft Guide Note –
Plumbing: Braided Flexible Hose Connections
– listing requirements for the use of Flexi
Hoses in all departmental projects. The Note
advises that “flexible connections are to be
the exception, not the rule.”
Another government agency, the
Department of Mines, Industry Regulation
and Safety in WA, issued a similarly styled
Technical Note several years ago –
Braided
Flexible Hoses
– designed “to assist
the plumbing industry to comply with
the prescribed plumbing standards and
manufacturer’s installation instructions
when installing braided flexible hoses.”
In Victoria, WorkSafe issued a safety
alert in May 2020 on the
Safe selection and
use of flexible hose assemblies,
explaining
that “WorkSafe is issuing a reminder about
the risks with using unsuitable flexible hose
assemblies at dangerous goods facilities
following two recent incidents that resulted
in loss of containment.”
We can only wonder: would such
advisories be necessary if regulators
enforced product compliance?
that all fittings must pass as part of the
WaterMark certification process.
Michael Glover says these strict
protocols, however, are often
sidestepped or ignored, or degraded
once WaterMark certification has been
approved with a ‘golden sample’ (i.e.
a high-quality sample used to gain an
initial accreditation; subsequently,
product quality is degraded for mass
production).
Non-compliant Flexi Hoses cause
millions of dollars’ worth of damage to
Australian homes every year.