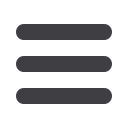
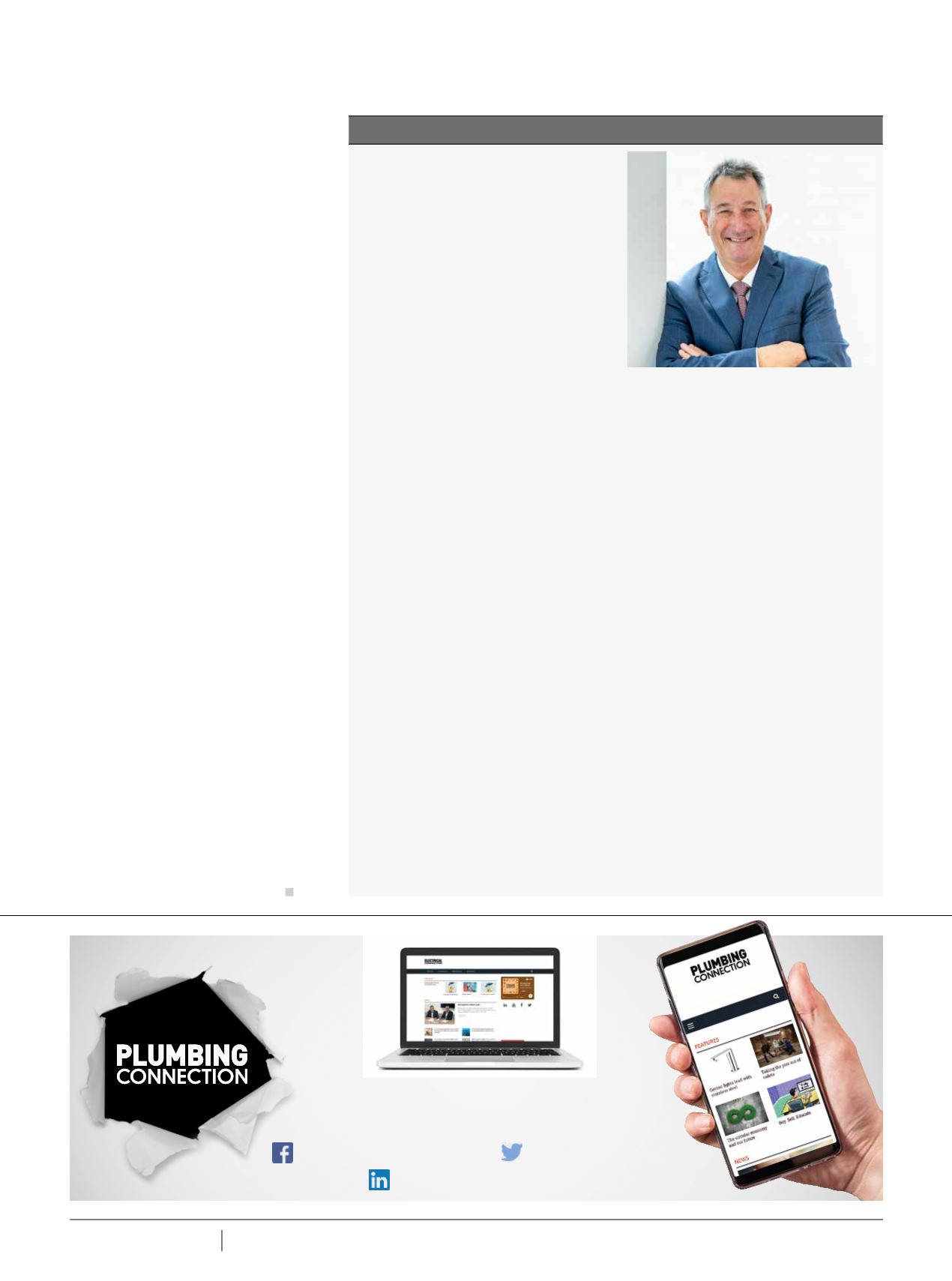
2 2
PLUMBING CONNECTION Winter 2022
20,000 checklists they have to do for
that project.” (Electrical and HVAC
specialists might each handle checklists
of similar magnitude.)
Without a real-time digital QA
process, extensive checklists can be
forgotten, deferred to a later date, or
simply sidestepped. “If a checklist is
done after the fact, it actually serves
very little function,” Daniel adds.
“So, our philosophy is to focus on our
customers, and to make it as easy as
possible for that site supervisor or end
user supervising their crew to do these
checks.”
Ease of use is a critical component
of any workplace QA platform, as
large numbers of contractors and
subcontractors with varying levels of
competence using new technologies
need to get up to speed quickly and
painlessly.
“Simplicity is probably our biggest
asset because you get engagement,”
Daniel reiterates, explaining that even
senior tradespeople generally have no
difficulty coming to grips with checklist
processes. “We offer training anyway,
so useability is not really an issue.”
CONQA clients like Lend Lease,
Multiplex, Scentre Group, Kapitol Group,
and others are clearly forging new
trends in the adoption of digital QA
platforms. And even though most major
construction works continue to depend
on paper-based QA records, the balance,
as mentioned, is shifting.
“In Victoria, we’re seeing
significantly fewer quality issues when
subcontractors use CONQA,” says Matt
Monger, QA Manager at Multiplex.
DIGITISING ALL PHASES OF CONSTRUCTION
Some construction companies are using
digital platforms to not only control QA, but
also to manage all collaborative aspects
of construction from design through to
handover.
A good example is the construction giant
Hansen Yuncken, which is in the final stage of
implementing Autodesk’s BIM 360 cloud-based
project collaboration and management system.
Peter Salveson, CEO of Hansen Yuncken,
says this platform is designed for use across
all project phases.
“It has been a transformative change for
Hansen Yuncken, which commenced many
years ago when we first adopted BIM-based
processes and implemented Autodesk’s
“Classic” Field software, accessing daily data
for reporting into our internal SharePoint-
based management system, ‘HYway’.
“Using a cloud-based storage solution for
project documents allows our site teams to
access the most up-to-date versions of plans
and models on their mobile devices. Updates
from design consultants and subcontractors
are immediately visible to team members in
the field. Because the entire project team
is notified in real-time the instant a change
is made, this allows them to comment on
or question any points requiring further
clarification.
“Having a central cloud-based location
where all data can be surfaced is incredibly
powerful. Using Power BI dashboard
integration, BIM 360 makes it easy for our
teams to take multiple data sources and
use different templates to create reporting
dashboards. Dashboards can be tailored
to the site team, executives, and any
other stakeholder. This ensures the right
information is delivered to these teams in a
relevant and meaningful way.”
According to Peter, all contractors and
subcontactors working on a project are required
to use the platform: “Subcontractors can
view and action their allocated checklists and
‘Issues’ from their mobile devices, compatible
with both iOs and Android systems.”
Apart from streamlining workloads and
schedules, the platform is designed to
enhance safety by allowing the company
to communicate safety-specific checklist
templates, assign them to members, and then
identify any safety-related trends in the field
that might need specific attention.
“By adopting complete lifecycle software
systems,” Peter adds, “construction projects
can run more smoothly, information can be
more easily communicated, and the handover
process is seamless due to the power of
today’s connected construction software.”
Worker training is part and parcel of the
process to ensure all participants are using
the platform effectively.
Once a project is completed, the BIM 360
database is an invaluable time capsule of
each project’s full construction history,
which is highly important as a guide for future
maintenance works, renovations or additions.
“If the client scopes the contract digital
deliverables appropriately, the BIM data can
provide unparalleled insight into how buildings
function post-construction, especially for
things like MEP (mechanical, electrical, and
plumbing) and HVAC systems, energy usage,
and solar thermal performance,” Peter says.
“It can be an irreplaceable tool for building
operations and key to reducing lifecycle
costs, which are proportionally massive:
70%–80% of a building’s lifetime costs occur
after its construction. With teams working
within a shared intelligent model, elements of
operations and maintenance can be vetted in
advance.”
Peter Salveson, CEO Hansen Yuncken.
QUALITY ASSURANCE
GET THE WHOLE STORY
www.plumbingconnection.com.au www.facebook.com/tradieconnection www.linkedin.com/in/plumbing-connection/ www.twitter.com/PlumbingCXNMag