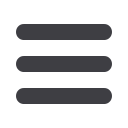
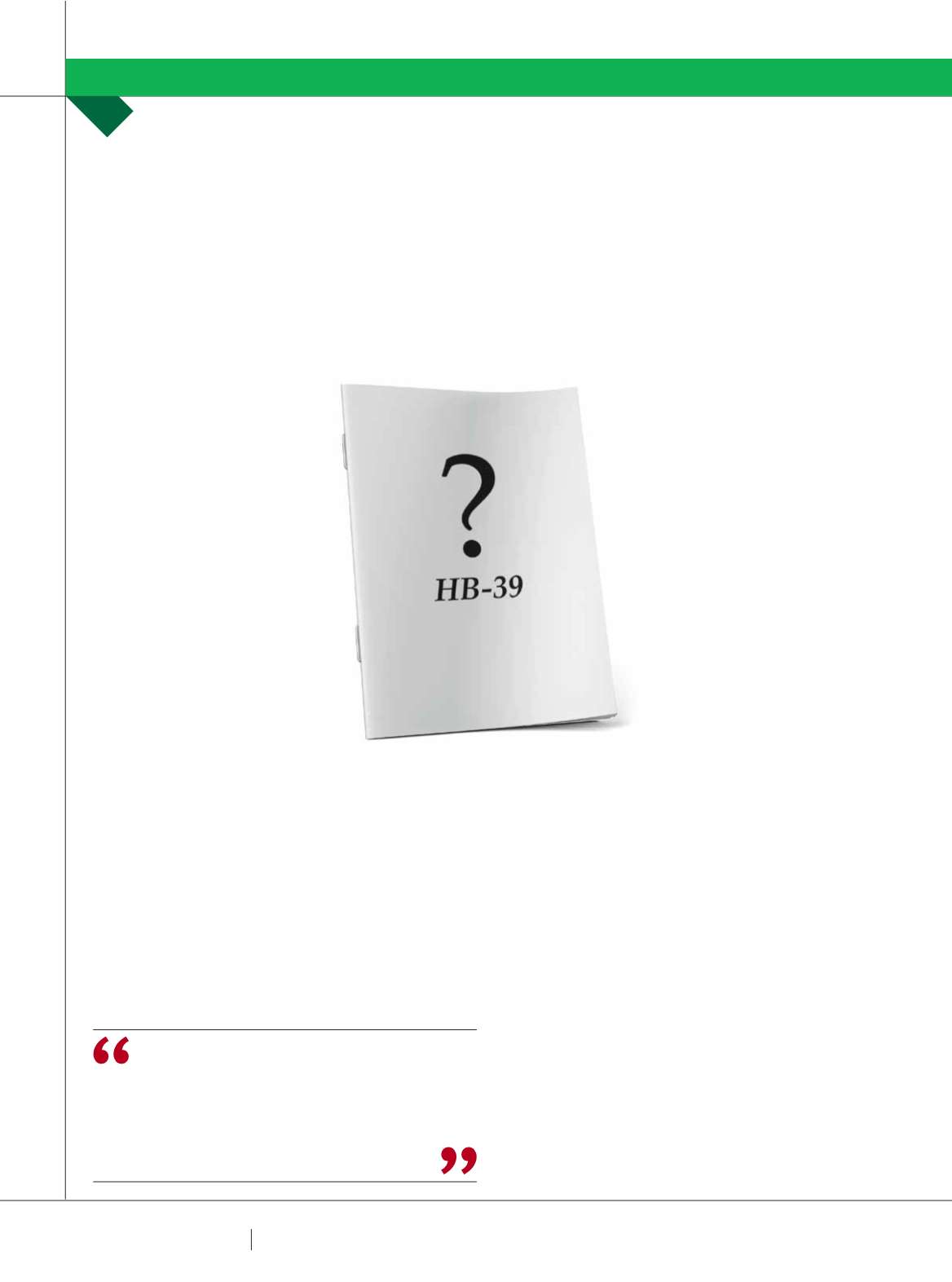
2 8
PLUMBING CONNECTION
WINTER 2015
METAL ROOFING
THE REVISED VERSION TAKES
INTO ACCOUNT THE EXISTENCE
OF THE LATEST STEEL COATING
TECHNOLOGIES IN THE MARKET.
INDUSTRY HANDBOOK GETS A TIMELY UPDATE
Our thanks go to Matt Wilson of the Victorian Building
Authority who is a member of the Standards committee that
reviewed and updated the popular handbook
HB 39 – 2015
edition, the
Installation Code for Metal Roofing and Walling
.
Matt supplied us with this overview of some points that have
changed with this new edition.
The handbook has been updated to introduce emerging
coating technologies and to reinforce appropriate
installation practices that when utilised will ensure the
installation of the roof coverings
and flashings are watertight.
If you’ve not previously had a
copy of this reference, the intention
of the handbook is to provide
basic installation guidelines and
acceptable standards of good
practice for use by metal roofing
installation contractors as well as
training providers in any State or
Territory. The general design and
sizing principles of roof drainage
systems indicated in HB 39—2015
may also be utilised when installing
drainage outlets, downpipes and
overflow provision in above-ground
external areas of buildings such as
drains from balconies, patios and the
like.
The revised version was prepared
by a steering committee and peer
reviewed by industry participants and is intended to
supersede
HB 39—1997 Installation code for metal roof and
wall cladding
.
The revised version takes into account the existence of
the latest steel coating technologies in the market.
Here are a few points that the revision covers and as you
will read, you’ll be well advised to get your hands on a copy
and study it in detail.
∫
1 IN 100 YEAR RISK
With more frequent and heavier storm weather; you need
to ensure you fully understand the latest guidelines for the
design of eaves and box gutters as well as roof drainage,
flashings and cappings. They’re in this handbook and it must
be referenced back to the relevant parts of your copy of AS
3500. You’ll also find some handy box gutter recommended
design examples for commercial, industrial and residential
projects.
∫
BOX GUTTER PRINCIPALS
The revision reminds roof installers of basic design
principles for box gutters so that gutters are designed
to have a constant width base (sole) with
vertical sides and where appropriate
constructed with a constant width base
(sole), single vertical side with lear, double
vertical side with lear or single or double
lear extending under the roof coverings
provided the effective area of the gutter is
appropriately sized for the roof catchment
area.
∫
STRAIGHTENING THINGS OUT ABOUT
GUTTERS
There is advice that box gutters are
to be constructed so to be straight
(without any change of direction) and
are to discharge at the downstream
end without any change of direction
(i.e. not to the side) and that V-shaped
gutters are not to be used.
Soaker gutters of adequate strength
appropriately sized for the roof catchment area above
penetrations are to be installed so that all roof water is
collected and drained into two or more full trays at the
sides of the penetration with waterways upstream of any
penetration to be not less than 100mm.
Eaves gutters with higher fronts than backs and eaves
gutters that could potentially discharge overflow into any
building are to be provided with fixed overflows calculated in
accordance with AS/NZS 3500.3.
Spreaders may be used to drain rainwater from higher
roof surfaces with catchment areas not exceeding 15m2
and may only exceed 15m2 provided the additional upper
roof discharge does not exceed the lower roof profile
manufacturer’s design carrying capacity.
∫
MENTION OF INSULATED ROOF PANELS
A typical description of an insulated panel (sandwich panel
or composite panel) is given that refers to building cladding
panels having metal facings to both surfaces, with an
insulation core completely filling the space between the two
facings permanently bonded to them both. Installers are
to refer to manufacturer’s specifications when selecting,
installing and working safely with these products.