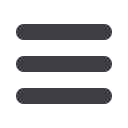
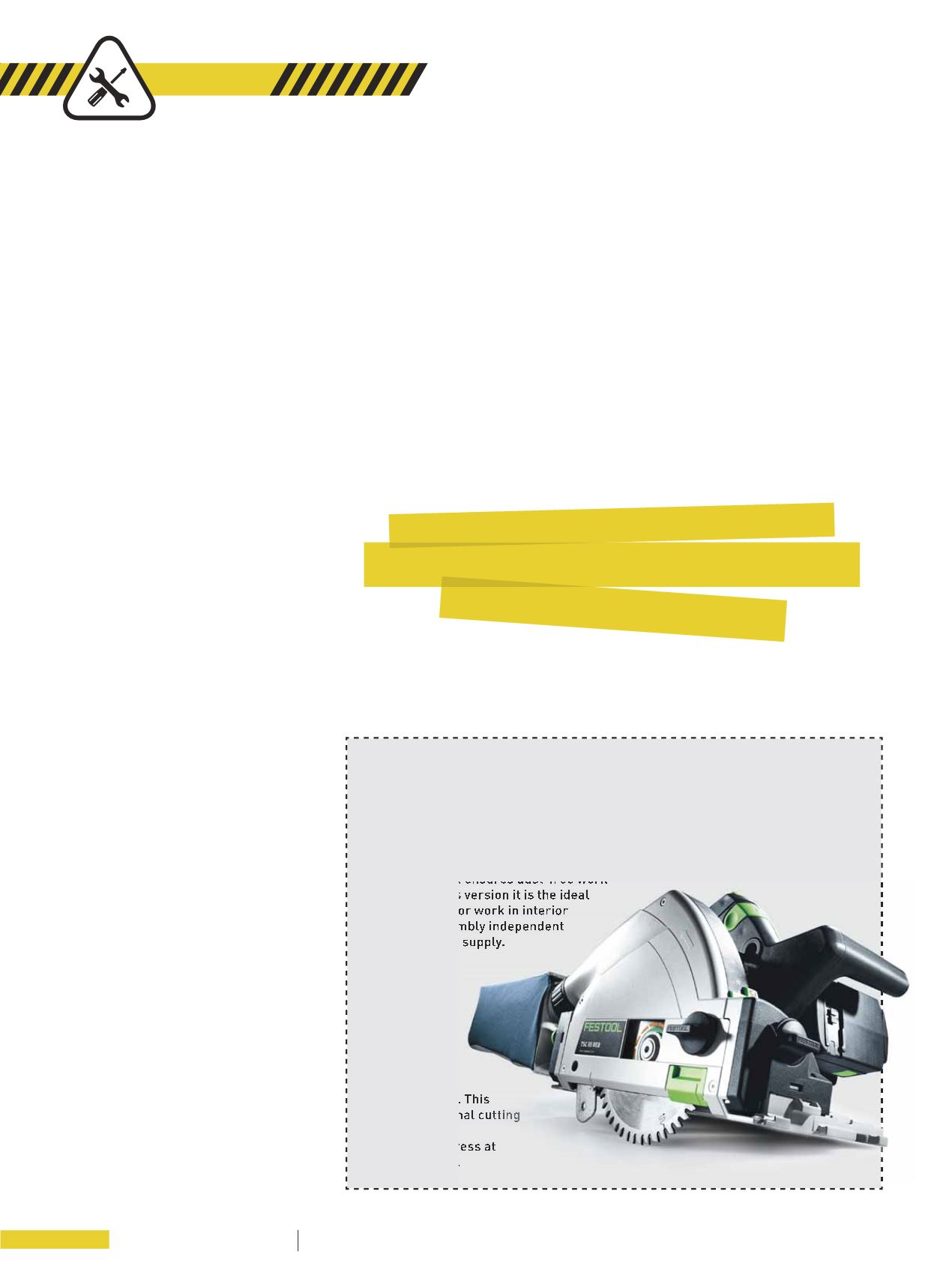
9 0
P L UMB I N G CO N N E C T I O N
A U T UMN 2 0 15
B
rushless motor technology is a
relatively new innovation in the
world of cordless power tools,
and it’s important to understand the
associated benefits.
Brushless motors reduce friction
caused by the internal brushes to
provide longer motor and battery life.
The reduced friction also allows for
more torque and power, as well as a
more consistent performance, making
it a truly ‘smart’ tool.
“A traditional brushed motor uses
carbon brushes, which make contact
on the motor to complete the circuit
and power the tool,” Hitachi Power
Tools assistant product manager
Justin Woolgar explains.
“Brushes wear and occasionally
need maintenance for replacement.
The mechanical contact of the brushes
on the motor causes electrical loss
and frictional resistance, as well as
heat build-up and contact wear – all of
which rob the motor of performance
and decrease durability.”
Further, he says, a mechanical
contact switch must be used to control
the increased and decreased flow of
electricity to the motor, which causes
further electrical loss and wear.
“Now, Hitachi brushless motors, for
example, use a micro-processor which
controls the current flow through the
motor. This means there are no carbon
brushes, which reduces maintenance
and unexpected downtime.
“Due to the lack of mechanical
contact on the motor, minimal heat
and motor wear occur. This results in
vastly improved electrical efficiency
and power transfer. An optical switch
is used to communicate with the
micro-processor, providing a more
responsive variable speed actuation
and wear-resistant switch assembly.”
Located beneath the tool grip,
the micro-processor chip manages
the tool’s motor and makes the tool
capable of advanced digital speed
settings for ultimate precision and
control by the user, Justin says.
“Electronic switches are more
efficient in transferring energy and
only require half the pull force of
conventional switches. This results
in longer battery and tool life, while
reducing user fatigue and discomfort.”
Festool cordless drills also use
brushless motor technology, which
the company is calling EC-TEC
(or ‘electronically commutated
technology’) motors.
“The biggest difference between
the latest EC-TEC motors and the
conventional DC brush motor is that
EC-TEC motors do not use carbon
brushes,” the company says.
DON’T GIVE BRUSHLESS
MOTORS THE BRUSH OFF
More and more power tools are
being marketed with brushless
motor technology, but what is
it?
Paul Skelton
reports.
Due to the lack of mechanical
contact on the motor, minimal heat
and motor wear occur.
TSC 55 CORDLESS PLUNGE-CUT SAW
Festool
www.festool.com.auPrecise, quick and guided cuts with lots of power and no cable? Not a problem with
the new cordless plunge-cut saw TSC 55 from Festool.
Festool has equipped its new TSC with a brushless EC-TEC motor and dual battery
concept for operation up to 36V. Together with
a new dust bag, it ensures dust-free work
and as a cordless version it is the ideal
plunge-cut saw for work in interior
fittings and assembly independent
of a mains power supply.
At 5,200
revolutions
per minute, the
new plunge-
cut saw has
a 24% higher
speed than
conventional
cordless
plunge-cut saws. This
guarantees optimal cutting
quality and
quick work progress at
the highest level.
TOOLS