Bursting the flexi-hose bubble
According to research conducted by general insurer IAG, flexible braided hoses accounted for 22% of water damage claims in Australian households in 2016, with the claims most likely to be for kitchen and bathroom damage. IAG has even labelled flexible connectors a ‘ticking time bomb’ and put notices on its website advising home owners that flexible hoses have a lifespan of between five and ten years, and should be checked by a licensed plumber every two years.
However, it’s unlikely consumers will heed this warning and it seems the onus is on the plumbing industry to collectively work together to do something about this issue.
In late July, Plumbing Connection organised a Flexible Connector Workshop in Melbourne with a range of industry stakeholders to discuss what product types are failing and in what applications, the influences that lead to product failure and how to ultimately reduce the incidence of failures.
The aim of this workshop was to start the discussion process about ways the plumbing industry can take the issue forward.
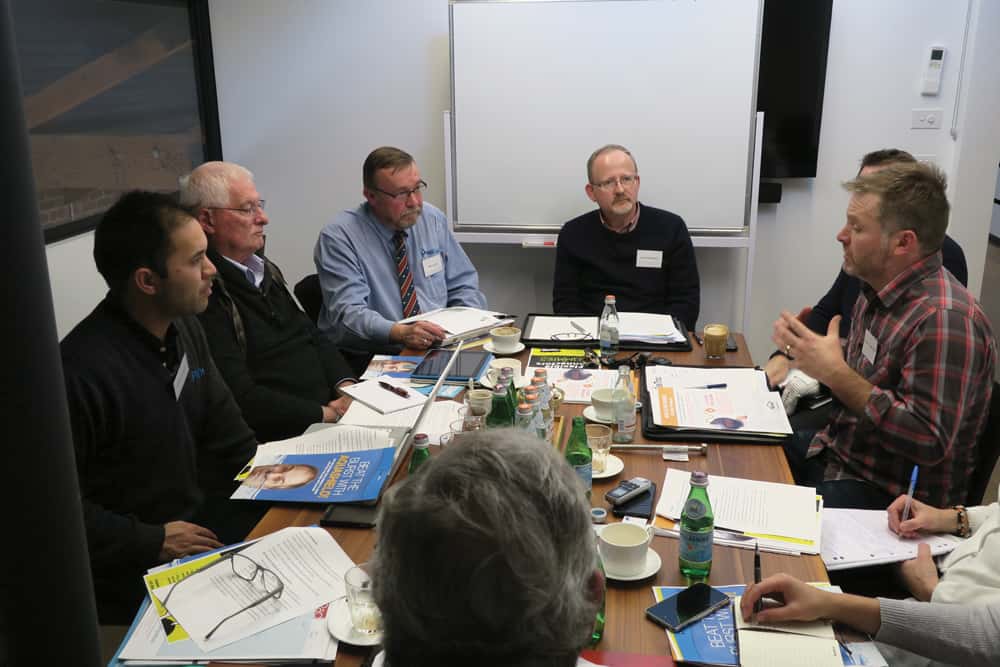
In July Plumbing Connection hosted a workshop with industry stakeholders to discuss the issue of bursting flexible braided hoses.
The following people attended:
- Abey Australia general manager Geoff Anderson
- PROVE Standards and Engineering plumbing test consultant Terry Nguyen
- Metropolis Solutions chartered loss adjuster David Pockett
- Metropolis Solutions forensic plumber Russell Kirkwood
- IAPMO Oceania technical manager Glenn Tate
- Shinners Plumbing owner and Master Plumbers Association (MPA) Victoria vice president Kevin Shinners.
- Aquaknect Flexibles general manager Tom Davies
- Our thanks go to the attendees for their time.
The emergence of flexible connectors
The first braided stainless steel flexible hoses came onto the Australian market as far back as 25 years ago and quickly became popular with the plumbing industry. Made from ethylene propylene diene monomer (EPDM) rubber or PEX and armoured in braided layers of stainless steel, these hoses replaced standard copper pipe installations from wall outlets to taps in kitchens, bathrooms, hot water services and laundries. This article primarily focuses on the performance of the EPDM tube version.
Flexible hoses are very versatile and significantly reduce the time it takes to hook-up hot and cold water pipe appliances, such as taps, dishwashers and water heaters. They also overcome alignment problems and significantly reduce labour costs and noise in pipe work, as well as eliminate brazing, welding, cutting, re-shaping and waste.
Over time, the popularity of these connectors has lead to them being included with the supply of many tapware ranges, whether mixer or hob mounted, and other fixtures. There are now approximately seven million flexible connectors sold annually in Australia and some of these are low-cost products from as little as $3-$5 from hardware stores.
Recent data released by insurance companies, including NRMA Home Insurance and general insurers IAG, QBE and Budget Direct, shows flexible braided hoses that have leaked or split are the number one cause of internal flooding in Australian homes.
NRMA Home Insurance says the average claim for escape of water in 2016/2017 was $4,818 (excluding excess and GST) but there have been reports of some claims costing tens or hundreds of thousands of dollars.
IAG executive manager for short tail claims Cheryl Chantry says properties between 11 and 30 years old are most likely to suffer an escape of water claim as flexible hoses generally only last 10 years. Yet the experiences of attendees at the workshop suggest some flexible hoses are bursting within a couple of months of installation.
Working out why this is happening and how it can be prevented isn’t as simple as pinpointing one cause and one solution.
It’s important for the plumbing industry to start a discussion and begin educating plumbers, manufacturers, TAFEs, insurers, regulators, government and consumers about the risk of flexible hose burst failure.
Bursting at the seams
Based on analysis of burst flexible connectors, it seems to be the braided stainless steel component of the product that is failing.
The rubber tube lining in flexible connectors expands when pressurised and the braided layers of stainless steel are designed to prevent this tube from further expansion. If the stainless steel fails, the rubber inner core will expand to a point where it bursts.
“This is primarily caused by a slow leak at the connection point, which runs down the hose into the braided stainless steel and leaves a deposit of chloride. Over time these chloride levels increase in the deposit creating pitting corrosion. The pitting locally reduces the cross-section of the wires to a point where overload failure occurs (due mostly to the hydrostatic water pressure),” says Metropolis Solutions forensic plumber Russell Kirkwood.
Chloride is present in natural waters from the dissolution of salt deposits and as a result, Australian drinking water has low chloride levels of up to 350mg/L.
Abey Australia general manager Geoff Anderson says that generally the 60/60/60 rule will enable stress corrosion cracking to occur. This is where water temperature is 60° with 60ppm of chloride and 60% of yield stress.
“Once the water reaches 60°, the evaporation process leaves behind a deposit of chloride. Over time the process continues and the chloride level increases in the deposit until it reaches a level that enables localised corrosion of the stainless steel to occur. Since the cracks caused by stress corrosion cracking are so fine, they are difficult to detect,” says Geoff.
This corrosion eats away at the individual metal strands of the steel sleeve, which eventually fail and break. When enough of these strands fail, the steel sleeve is no longer able to support the inner lining and water pressure causes the lining to bulge out of the sleeve. This leads to the lining rupturing and water escaping.
The presence of water exterior to the hose is required for corrosion, which is why most failures are seen under kitchen, laundry and bathroom sinks, toilets and dishwashers, rather than on connectors to gas stove cook-tops.
Materials Solutions Australia (MSA) engineering director Trevor Rowlands says pulling apart burst flexible connectors clearly shows the moisture path and evidence of corrosion.
“Stainless steel isn’t impervious to corrosion and can become vulnerable when put through certain conditions. However, the stainless steel braiding is appropriate for its function and it’s the leakage at the connection that is the issue. You can always trace a leak path in these hoses and all the ones I’ve seen have had a leak path at the connector.”
Why is this happening?
There are various reasons why this leakage occurs but four main issues arise based on experience in the field. These are installation, the effects of water hammer, the quality of materials in the manufacturing process and household cleaning products being stored within the vicinity of flexible braided hoses in homes.
Other than poor quality, the majority of these reasons are not due to the connector itself, which suggests the issue of bursting flexible hoses is largely preventable.
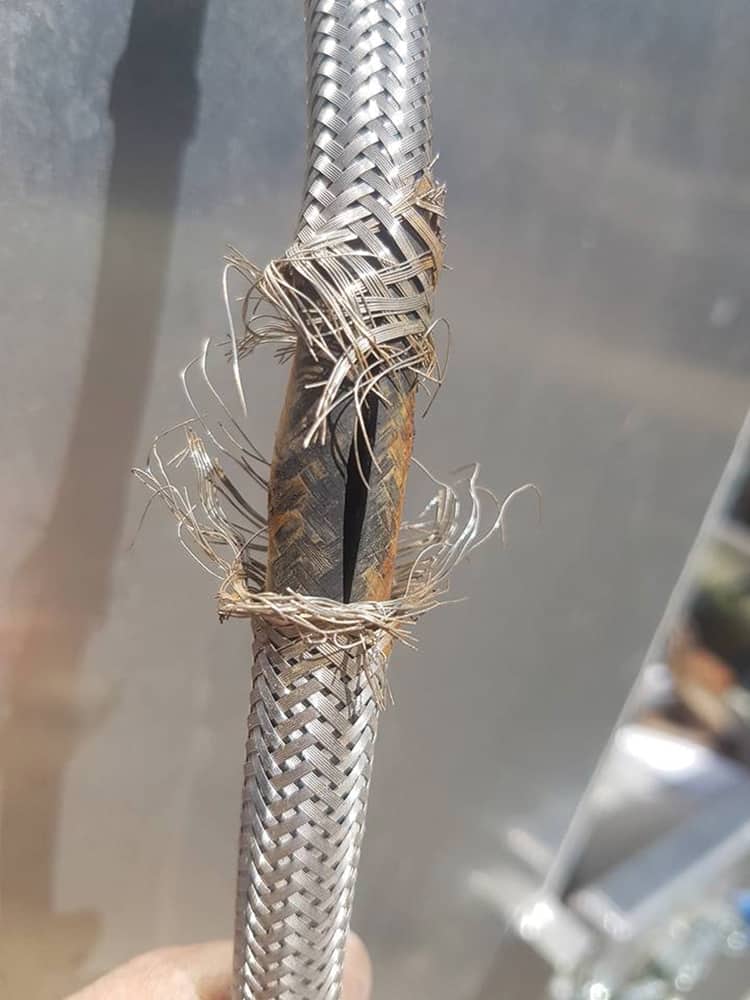
The stainless steel braided sleeve corrodes, causing the rubber inner tube to expand and burst. Image supplied by Neil & Craig Baker Plumbing – NSW.
Installation
Russell and Trevor both suggested installation issues are playing a big role in bursting flexible braided hoses, particularly in regards to the tightening of the nuts at either end of the connectors.
“Where the nut is connected at one end under the sink or to the mains water its fine but when it comes to tightening up the second nut, which connects to the tap assembly, the design is such that the first nut can become loose,” says Trevor.
“When you tighten the first nut, the second nut can actually partially loosen off again if the ferrule isn’t gripped or held at the first end.”
This slight loosening leads to a slow leak that allows water to migrate across the rubber seal face down to the back face of the nut and eventually onto the braiding.
Tightening the nuts is also an issue where the installing plumber hasn’t torqued one or both of the nuts sufficiently. If it’s too loose it creates a leak path and if it’s too tight the seal will rupture.
“These end in the same result, which is corrosion of the stainless steel braiding, leading to wire breakage and then the rubber tube expanding and bursting,” says Trevor.
The rise of the DIY culture in Australia and the low cost of these connectors are also increasing the likelihood of flexible hose failures, as they encourage handymen to attempt installations themselves.
General insurer Budget Direct says on its website that this is compromising the integrity of flexi hoses in homes as DIY is more likely to result in flexible hoses being damaged at the time of installation, which then increases the chance of bursting.
There are fears that eventually insurance companies will begin disallowing claims if customers can’t prove installation by a licensed plumber as well as regular maintenance.
“There’s a significant risk here for the home owner and it’s likely to get far worse given the high rate of losses insurers are currently reporting due to these flexible connectors,” says Metropolis chartered loss adjuster director David Pockett.
Effects of water hammer
Although by itself water hammer will not cause failure, it is a contributing factor that can play a role in the final catastrophic failure of a flexible braided hose once it has been brought to a vulnerable point.
Phillip Woolhouse has more than 30 years experience in the plumbing sector and is the principal consultant at Phil Woolhouse Hydraulics in Perth. He says the speed at which modern tapware can be isolated puts the rubber seal under constant force.
“Mixer taps can be closed in a fraction of a second and the faster the tap is isolated, the higher the pressure shock. Pressure well above 500kpa can be experienced by modern fast-closing tapware and this generates massive shock pressures within the piping system.”
According to Trevor, this can cause the rubber seal to react by compressing over time and forming a permanent stress.
“Some rubber does have a memory effect and will shrink. Over time this loosens the nut and there’s less contact pressure on the seal face, allowing water to leak.”
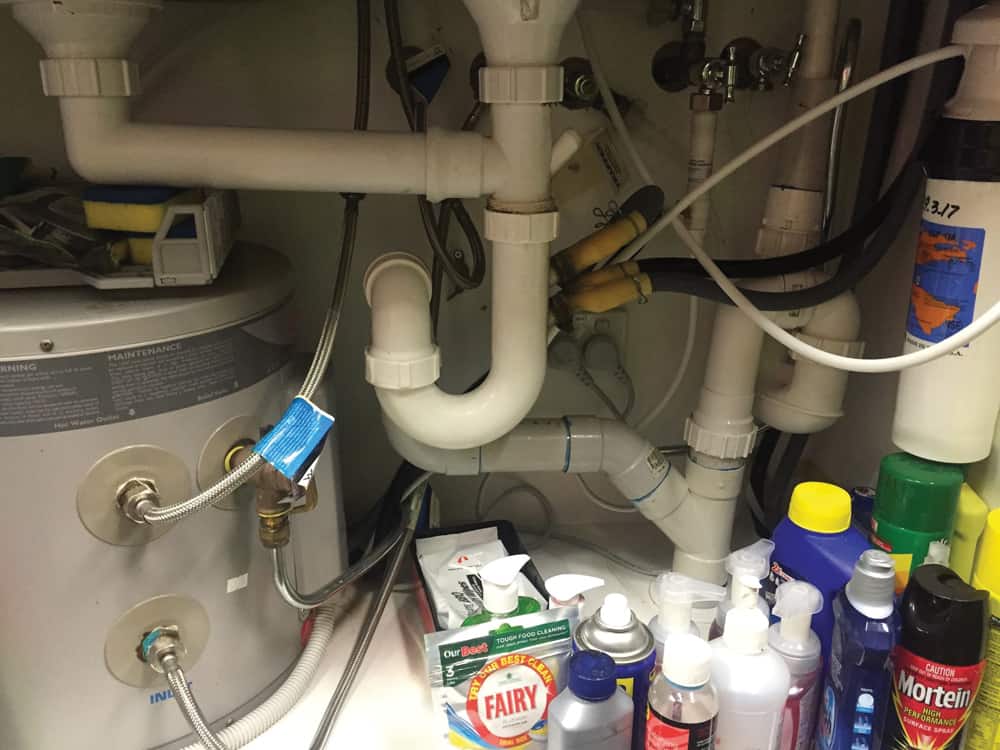
Common household cleaners stored under kitchen or bathroom sinks where flexible braided hoses are installed can create fume cupboard environments that corrode the braided stainless steel sleeve, leading to bursting hoses.
Quality of materials
With the price of flexible braided hoses continuing to drop and a number of new products entering the market, there are concerns that the quality of steel and brass components being used in some hoses are contributing to the early failures being seen in the field.
Trevor says he has come across flexible braided hoses where the brass barb fittings were not properly manufactured or heat treated.
“Alpha-beta brass had been used, which is cheaper but more susceptible to de-zincification corrosion, and had not been carefully controlled during the manufacturing and thermal cycling process. The aim is to produce a microstructure with ‘islands’ of beta phase but when they interconnect, forming a continuous network, once corrosion occurs it creates a continuous pathway allowing water to pass through the cross-section of the barb fitting from the inside to the outside surface. The water is then in direct contact with the area where the rubber tube of the hose and the stainless steel braiding are crimped.”
Aquaknect Flexibles general manager Tom Davies says he also has concerns about the wire size being used on the braiding as a weaker braid is more likely to fail. The company, which is an Australian manufacturer of flexible braided connectors, uses a minimum wire size for braiding of 0.23mm.
“This is the minimum for us but there are some manufacturers where the largest wire is 0.15mm, which is 33% thinner, and you can see through the gaps to the rubber underneath. With the tap being turned on a few thousand times, the hose flexes back and forth, causing a weaker braid to fail regardless of whether the braid has broken,” says Tom.
“Additionally, less mass means quicker corrosion.”
There are suggestions that these low-quality products are able to make it to market by unscrupulous suppliers that are defrauding the WaterMark product certification system with what’s known as the ‘golden sample’.
The ‘golden sample’ is when a product supplied for third-party testing is of a high enough quality to pass requirements but the product supplied when large orders are placed is substituted with a low-cost alternative.
Fume cupboards
Common household cleaners kept under sinks and cupboards create a ‘fume cupboard’ environment in areas where flexible braided hoses are installed and is a potential second source of corrosion causing flexible connectors to burst.
The presence of stored household cleaners in closed environments causes the level of chlorine in the air to rise to measurable levels because many common cleaners contain chlorinated chemical solvents, liquid chlorine or crystallised chlorine chemicals. These remain in the air long after the product has finished being used.
“In most cases cleaning products are stored in bathroom, kitchen or laundry sink cabinets where there is high humidity caused by condensation from hot water being run through the taps and bowls above the cabinet,” says Tom.
“Chlorine dissolves in humidity and forms hydrochloric acid, which is highly corrosive. Therefore the number of failures in this environment caused by corrosion is high.”
Cheryl from IAG says that the company’s research backs up this claim, with IAG data suggesting flexible braided hoses eroded faster if household cleaners are stored under the sink.
Plumbing industry response
Starting a discussion about the issue of bursting flexible braided hoses is an important first step but action needs to be taken to bring the problem to the attention of regulators, government, TAFE’s, manufacturers and consumers.
“It’s still only a small percentage of the industry that realises this issue is happening,” says Trevor.
At the workshop hosted by Plumbing Connection, there was consensus that the current AS/NZS3499:2006 Water supply – Flexible hose assemblies needs to be updated.
“Changes to the Standard need to reflect technology and practicality. The current version was last reviewed in 2006, with a small amendment in 2009, and since then there have been many regulatory and technological changes,” says Tom.
There are also concerns that manufacturers are actually writing their own interpretation of the Standard, with one supplier on the shelves of a prominent Australian outlet providing a selective product warranty that “covers domestic use only and not for commercial applications”.
Representatives at the workshop discussed the possibility of proposed changes to the Standard, including introducing a minimum wire diameter for the stainless steel braid, future testing for things like corrosion, markings on the inner liner of hoses to identify manufacturer and changes to the classification of hoses.
Trevor agrees that there are things within the current Standard that are not ideal but says because many of the issues causing burst flexible connectors may be the result of incorrect installation, a change to the Standard will not have much of an impact.
“The manufacturers and suppliers of these hoses need to implement specific requirements about how flexible hoses are installed and maintained. I think that’s probably going to solve a lot more problems compared to the Standard.”
Regardless of how the industry decides to take this issue forward, it’s important that action is taken soon.
“Unless the whole industry gets together and does something, we will still be talking about this in a few years,” says Shinners Plumbing owner Kevin Shinners.